Emission Estimation Technique Manual
3.1.3 Emissions to Air and Estimation Techniques 9 3.2 Secondary Metal Processing and Alloy Production 13 3.2.1 Description 13 3.2.2 Emissions to Air and Estimation Techniques 14 3.2.3 Emission Factors for Secondary Metal Processing and Alloy Production 19 3.2.3.1 Secondary Aluminium Operations 19 3.2.3.2 Secondary Copper Smelting Operations 19
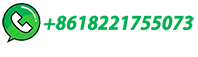