Finish Mill Cement Plant | Crusher Mills, Cone Crusher ...
finish mill grinding cement production process | Ore Mining. Cement grinding plant includes all kinds of powder mill. – Get More or Get Price – …
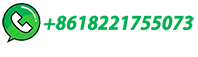
finish mill grinding cement production process | Ore Mining. Cement grinding plant includes all kinds of powder mill. – Get More or Get Price – …
The vertical mill cement grinding power consumption is low, grinding cement does not need auxiliary cooling, and the residence time of the material in the mill is very short, can quickly convert from one species to another species, does not need to be a lot of grinding material out, but also in the production process of rapidly changing product ...
The plant was first upgraded in 1956 with the addition of a fifth, and much larger, wet process kiln, increasing clinker capacity by 25%. In 1995, a major upgrade occurred in the finish grinding department with the installation of a 4400-HP mill to take the place of the five smaller mills.
two different cement types were ground Figure 2: process flow sheet of slag mill Figure 3: process flow sheet of cement mill Figure 4: process flow sheet of cement mill in RP finish mode Table 3: composition of CEM II and CEM IV cements Parameter CEM II CEM V Clinker (%) 84.6 40.5 Gypsum 4.9 4 Limestone 4.8 4.5 Slag 5.7 25 Trass 0 26
• Roller press in semi finish and finish grinding mode • Vertical roller mill (VRM) • Ring roller mill or Horo mill Even though there are various types of systems available for cement grinding, ball mills are predominantly used machines for cement grinding in large number of cement plants. In this paper authors are covering the process
Cement manufacturing - brief description of a cement mill. Cement clinker is usually ground using a ball mill. This is essentially a large rotating drum containing grinding media - normally steel balls. As the drum rotates, the motion of the balls crushes the clinker. The drum rotates approximately once every couple of seconds.
Whether your applications involve the lubrication of crushers, mills, grinding rollers, kilns or excavators, FUCHS is the strong and reliable partner for you, providing solutions for all requirements of the cement industry - including all relevant approvals.. We want your machines to perform at high-level – every day. With FUCHS, you can enjoy the full range of high …
production by cement clinker grinding. Production costs and environmental concerns are emphasizing the need to use less energy and require design updating in the ball mill components. For most of the twentieth century, the dry grinding circuits for the production of finished cement from cement clinker consist of two-compartment tube mills and ...
Our Cement Mill Optimizer system, is a parallel intelligent solution that acts as an autopilot for the cement grinding circuit. It optimizes the cement quality and increases the overall production by keeping the cement product fineness closer to the ideal targets or in other words keeping a low standard deviation of the final product particles ...
Stage 4: Finish Process Greater Detail: Cement Plant Operations Handbook Crewmen's Guide, Finish Mill Systems Cement mill A 10 MW cement mill, output 270 tonnes per hour A cement mill (or finish mill in North American usage[1]) is the equipment used to grind the hard, nodular clinker from the cement kiln into the fine grey powder that is cement.
World total cement production for 2016 was about 4.2 billion tons with emerging markets playing a dominant role (IFC, 2017). The energy intensity of cement production ranges from 3.6 to 6.5 GJ/ton depending on production process and location of the production (Hammond and Jones, 2011; Ohunakin et al., 2013; Worrell et al., 2000).
crushing or grinding cement finish mill processes through patented, industry-leading technology. Monitor and Control Monitoring and controlling production can significantly reduce process variability, increase overall production rate …
• Roller press in semi finish and finish grinding mode • Vertical roller mill (VRM) • Ring roller mill or Horo mill Even though there are various types of systems available for cement grinding, ball mills are predominantly used machines for cement grinding in large number of cement plants. In this paper authors are covering the process
Cement Finish Raymondgrindingmill. Know More Cement finish grinding with roller press Page 1 of 1 Cement finish grinding with roller press What about the water demandof a cement grounded in a [Get More] Get Price And Support Online. cement industry finish grinding process. Raw mills usually operate at 72-74% critical speed and cement
11.6 Portland Cement Manufacturing 11.6.1 Process Description1-7 Portland cement is a fine powder, gray or white in color, that consists of a mixture of ... to the process during the finish grinding operations described below. These materials, also excavated ... water is added to the raw mill during the grinding of the raw materials in ball or ...
A cement mill is also applied for grinding clinker into finished cement. The cement clinker grinding is the last step of the cement manufacturing process, in this step, cement mill grinds cement clinker, gelatinizing agent and other materials into the required size, which can meet the requirement of cement.
Cv cont ent at Kiln inl,·, Fig. 4 Process Variables for Kiln Control Optimization of Cement Manufacturing Process grinding efficiency Fig. 5 An example of detection of coating ring fall Fig. 6 optimum set point mill sound level Grinding Efficiency of Ball Mills feed back action raw meal composition control kiln control l I r Supervisory System ...
In the cement production line, producing 1 ton of Cement need grind at least 3 tons of materials (including raw materials, fuel, clinker, mixed materials,gypsum).Grinding operation consumes about 60% of total power in cement plants, raw material grinding more than 30%, while coal mill used in cement plant consumes 3%, cement grinding about 40%.
The finish mill system in cement manufacturing is the second to last major stage in the process, where the feed material is reduced in size from as large as several centimeters in diameter, down ...
Step 6 : Finish Grinding. The clinker is ground in a ball mill—a horizontal steel tube filled with steel balls. As the tube rotates, the steel balls tumble and crush the clinker into a super-fine powder. It can now be considered Portland cement. The cement is so fine it will easily pass through a sieve that is fine enough to hold water.
A 10 MW cement mill, output 270 tonnes per hour. A cement mill (or finish mill in North American usage) is the equipment used to grind the hard, nodular clinker from the cement kiln into the fine grey powder that is cement. Most cement is currently ground in ball mills and also vertical roller mills which are more effective than ball mills.
planning to put up a new cement grinding plant using Vertical Roller Mill(300-350 – TPH) and before implementing the project, we would like to gather as much information regarding the actual operation of this mill during cement grinding and …
wet mill cement mill grinding ball mill. · Cement mill is the key equipment for grinding after the crush process, which is widely used in the manufacture industries, such as cement, silicate, new building material, refractory material, fertilizer, ferrous metal, nonferrous metal and glass ceramics, and can be used for the dry and wet grinding for all kinds of ores …
Finish Mill. The final process of cement making is called finish grinding. Clinker dosed with controlled amount of gypsum is fed into a finish mill. Typically, a finish mill is a horizontal steel tube filled with steel balls. As the tube rotates, the steel balls are lifted, tumble and crush the clinker into a super-fine powder.
Finish mill #11 was a standard ball mill, capable of producing approximately 90 tons per hour of type I/II cement. Finish mill #10 was a ball mill configured with a roller press for pre-grinding, capable of producing approximately 130 tons per hour of type I/II cement.
Raw Mill In Cement Production . Reducing energy consumption of a raw mill in cement Cement production in the world is currently about billion ton per year About 2 of the electricity produced in the whole world is used during the grinding process of raw materials While total electrical energy consumption for cement production is about 100 kWh/ton of cement …
Cement grinding mill is similar to that of Raw mill used for raw material finish grinding. There are 3 cement mills A, B and C mill with a clinker grinding capacity of 60 tph for A mill and 50 tph each for B mill and C mill. The B and C mills are identical in construction. A mill has got 2 chambers and for B & C mills 3 chambers each. Flint ...
Module 2 – Ball mills. This module will cover the technology of ball mills used for raw and finish grinding in the cement manufacturing process. * Mechanical description of the different types of mills. * Ball mill grinding equations and dimensioning. * Mill internals, media, liners and diaphragms. * Ventilation, cooling and drying. * Control ...
1. Production process of cement A cement clinker grinding plant consists of the following three processes. (1). Raw material process (2). Clinker burning process (3). Finish grinding process The raw material process and the clinker burning process are each classified into the wet process and the dry process.The raw material process and the clinker burning …
Finish Mill Grinding Cement Production Process. This article comes from Google search, if you want to know more detailed product information, please get in touch with … Finish Mill Grinding Cement Production Process | Process … Finish Mill Grinding Cement Production Process 35 Views. The is the professional mining equipments ...
حقوق النشر © 2024.Artom كل الحقوق محفوظة.خريطة الموقع