PART 3 INTRODUCTION TO ENGINEERING HEAT TRANSFER
HT-7 ∂ ∂−() −= f TT kA L 2 AB TA TB 0. (2.5) In equation (2.5), k is a proportionality factor that is a function of the material and the temperature, A is the cross-sectional area and L is the length of the bar. In the limit for any temperature difference ∆T across a length ∆x as both L, T A - T B → 0, we can say dx dT kA L T T kA
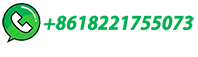