What are the powder metallurgy technologies - Hangzhou ...
It is completed in a high-energy ball mill and requires long-term grinding between powder particles and between powder particles and grinding balls. The powder will be broken and torn. The ultrafine powder preparation technology in powder metallurgy, due to the small particle size, the powder prepared by this technology has significantly ...
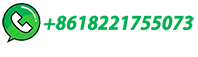