Refractory - Gaofu
The refractory raw materials need to be sieved after crushing and grinding. The refractory material can ensure the densest packing after passing through the vibrating screen to obtain a dense idiozome. Gaofu refractory vibrating screen manufacturer price consultation telephone: 86-373-5702900.
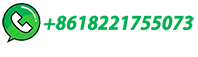