(PDF) Effect of Grinding Aids in Cement Grinding
Grinding process of clinker was carried on with a laboratory scale ball mill by varying different type of grinding additives and dosage while the operating conditions of …
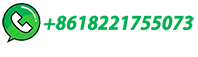
Grinding process of clinker was carried on with a laboratory scale ball mill by varying different type of grinding additives and dosage while the operating conditions of …
A cement clinker grinding plant consists of the following three processes. (1). Raw material process. (2). Clinker burning process. (3). Finish grinding process. The raw material process and the clinker burning process …
Great Wall Machinery (CHAENG), cement clinker grinding plant manufacturer
Grinding Aids reduce particle re-agglomeration during and after the milling process so improving the yield. Strength enhancers push clinker reactivity increasing the use of SCM in blended cements.
The overall process of conversion from raw meal to clinker being endothermic demands a theoretical heat of about 380-420 kcal/kg-clinker. However, the rest of the specific heat consumption as tabulated above constitutes heat losses from preheater exhaust gases, clinker, cooler exhaust gases, preheater dust and radiation losses.
The manufacture of cement is a very carefully regulated process comprising the following stages: 2.1. Quarrying - a mixture of limestone and clay. 2.2. Grinding - the limestone and clay with water to form slurry. 2.3. Burning - the slurry to a very high temperature in a kiln, to produce clinker. 2.4.
An exemplary process for grinding cement clinker using rollers comprises introducing cement clinker into grinding contact with rollers operative to grind the clinker into particles; and introducing to the clinker and/or rollers, in an amount of 0.001-0.5 percent based on the dry weight of clinker, a binding-densifying agent comprising at least one polymer having an …
Solution Features 1. Simple in technology process, saving capital construction investment. 2. Clinker Grinding Unit has powder separator, adopts hot air transport materials, the powder and gas enter into powder separator when out of mill.
Clinker Grinding Process. 1.Clinker Grinding System. Various materials are quantitatively given in the cement batching process according to the set ratio. After the materials are discharged proportionally by the feeding metering equipment, they …
The chemical grinding stabilizers that are linked up to the surface groups of cement particles resulting from the clinker grinding process participate in the hydration process. The rate of hydration is one of the key variables in the application of grinding additives in the cement industry. 3. Experimental. 3.1.
The evaluation of grinding aid (GA) effect on clinker processing in laboratory grinding mills is relatively simple. Yet, the results obtained cannot be directly transposed to industrial mills, given the fundamentally different operational modes and grinding parameters. This paper seeks to evaluate the scale effect by comparing the results obtained from a closed …
Clinker grindability is determined by quantity of electricity consumed for grinding (kW / ton) under other equal conditions. In cement …
Clinker production: There are various combinations of preheating and calcining systems, and which process is better depends on whether the existing plant needs to be rebuilt and how much the plant operators invest in the construction. The cement rotary kiln and cyclone preheater are the recommended group here.
used cement grinding plants for sale. cement grinding plant for sale expresspeb.be. 1000-5000tpd cement clinker grinding plant for sale cement clinker grinding plant is suitable for grinding the barite, limestone, kaolnite, ceram and slags, etc. which below scale 9.3 of Moth and below 6% shadness and 280-odd sorts of non-inflammable and non …
The clinker is then cooled and ground to a fine powder in a tube or ball mill. A ball mill is a rotating drum filled with steel balls of different sizes (depending on the desired fineness of the cement) that crush and grind the clinker. Gypsum is added during the grinding process to provide means for controlling the setting of the cement.
Only close economic study can determine which process should be used. CLINKER GRINDING. Clinker, the discharge product from the kiln, is partially cooled and broken or crushed to about ¾" – 1″ as feed to finish mills. Fineness of grind is dependent upon the type of cement to be produced.
Cement Production Process. The cement production processes mainly include raw material crushing and storage, raw material proportioning and grinding, clinker calcination, clinker grinding, cement packing, etc. Portland cement is …
The manufacture of Portland cement is a complex process and done in the following steps: grinding the raw materials, mixing them in certain proportions depending upon their purity and composition, and burning them to sintering in a kiln at a temperature of about 1350 to 1500 ⁰C. During this process, these materials partially fuse to form nodular shaped clinker …
Step 6 : Finish Grinding. The clinker is ground in a ball mill—a horizontal steel tube filled with steel balls. As the tube rotates, the steel balls tumble and crush the clinker into a super-fine powder. It can now be considered Portland cement. The cement is so fine it will easily pass through a sieve that is fine enough to hold water.
The cement manufacturing process consists of the following steps: Grinding and mixing of the raw materials. Burning of the mixture at a specified temperature for the correct duration. Grinding the consumed item called (clinker) along with gypsum. There are two methods available for the manufacture of cement: Wet Process.
What is the cement clinker? As we know, the cement production process is mainly divided into raw material preparation, clinker calcination, and cement grinding. Clinker is the material produced in the calcination stage and is usually used as …
A CLINKER GRINDING PLANT, engineering by LAXMI ENGINEERS, JODHPUR, INDIA
Applicability of oxy-fuel technology to clinker burning process • Oxygen production by air separation is state of the art (by freezing or membranes) • Oxy-fuel technology is state of the art in other industries, e.g. for glass production • New combustion technologies required, e.g.: – Oxy-fuel burner – Waste gas recirculation
HOLTEC has undertaken Performance Optimisation of the cement grinding circuits by doing process diagnostic studies in many cement plants. The paper describes the approach for the process diagnostic study for the optimisation of a ball mill circuit and is supported with typical case study done by HOLTEC in a 1.5 mio t/a ...
The last stage of making cement is the final grinding process. In the cement plant, there are rotating drums fitted with steel balls. Clinker, after being cooled, is transferred to these rotating drums and ground into such a fine powder that each pound of it contains 150 billion grains. This powder is the final product, cement. Stage 6
clinker grinding unit . On the other hand, clinker grinding may be the last step of cement production process. Therefore, cement griding system control, relates directly to cement product quality, yield, and value. On the other …
Cement production is also a highly energy intensive process, and particularly, the grinding of the cement clinker accounts for as much as 40% of the total production cost. Therefore, grinding additives are widely used by the cement industry as they can lead to a significant decrease of electrical energy consumption by about 10%.
A grinding aid composition suitable for grinding clinker into hydraulic cement powder, an improved grinding process and an improved cement product are disclosed. The grinding aid composition is composed of a mixture of at least one alkylene ether glycol and particulate carbon.
China 50t/H Portland Cement Grinding Plant/Clinker Grinding Unit, Find details about China Clinker Grinding Unit, Cement Production Machinery from 50t/H Portland Cement Grinding Plant/Clinker Grinding Unit - Henan Zhengzhou Mining Machinery Co., Ltd.
The process of clinkerization signifies conversion of raw meal into clinker minerals mainly consisting of C4AF (Aluminoferite), C3A (Aluminite), C2S (Belite) and C3S (Alite) phases along with small percentage of free lime CaO, MgO, Alkalies, Sulphates etc.
حقوق النشر © 2024.Artom كل الحقوق محفوظة.خريطة الموقع