THE INFLUENCE OF GRINDING MEDIA HARDNESS ON AN …
The top size of the grinding ball to be used in a wet ball mill grinding operation can be calculated by taking into account the feed size, product size, specific gravity of the ore, the work index of the ore, the mill diameter and the fraction of mill critical speed (8). Hardness of a commercial grinding ball produced is dependent
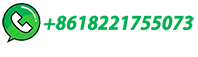