msds sheet for nickel laterite
msds sheet for nickel laterite - psychoterapeuta … 1 Product and Company Identification Product Name Copper Nickel Alloy Chemical Name Metal Alloy Synonyms Copper Nickel, UNS/CDA Alloy Nos. C70600, C71500, C72500, C72900, C75200 Chemical Family Copper Alloy Formula Not applicable - mixture Product Use Metallurgical Products Company Address Fisk Alloy PO …
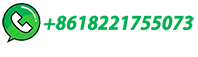